LVL (Laminated Veneer Lumber) formwork has emerged as the go-to choice for modern construction projects. Its numerous advantages and technological advancements have revolutionized the industry. In this article, we will explore the key aspects of LVL formwork that make it the preferred option in today’s construction landscape.
Understanding LVL Formwork
Before delving into the advantages, let’s start with the basics of LVL formwork. LVL formwork is a construction technique that utilizes laminated veneer lumber panels to create temporary molds for concrete structures. These molds define the shape and dimensions of the concrete elements, such as walls, slabs, and columns.
The recognition of LVL formwork sustainability benefits and its positive impact on project timelines and costs are driving its widespread adoption. With ongoing research and development, LVL formwork is poised to shape the future of construction, revolutionizing the industry and promoting sustainable construction practices worldwide.
LVL formwork consists of multiple layers of thin veneer sheets, typically made of high-quality softwood. These sheets are bonded together using adhesives, creating a rigid and durable material. The resulting panels are lightweight, stable, and easy to handle, making them ideal for various construction applications.
The Basics of LVL Formwork
In its simplest form, LVL formwork involves assembling the LVL panels to create the desired shape for the concrete elements. The panels are supported by vertical and horizontal beams, known as studs and wales, respectively. These components provide stability and ensure the formwork can withstand the pressure exerted by the fresh concrete.
But what happens after the formwork is assembled? Once the LVL panels are in place, the next step is to prepare the surface for the concrete. This involves applying a release agent to prevent the concrete from sticking to the formwork. Additionally, reinforcement bars, also known as rebar, may be installed to provide additional strength to the concrete structure.
Once the surface is ready, the concrete is poured into the formwork. This process requires careful attention to detail, as the concrete needs to be evenly distributed and compacted to ensure a strong and durable final product. Vibrators may be used to remove any air bubbles and ensure the concrete fills all the nooks and crannies of the formwork.
After the concrete has been poured, it needs time to cure and harden. This typically takes several days, during which the formwork remains in place to provide support. Once the concrete has reached its desired strength, the formwork can be removed, revealing the finished concrete structure.
One of the advantages of LVL formwork is its versatility. It can be easily adjusted to accommodate different shapes and sizes, allowing architects and engineers to bring their creative visions to life. Whether it’s curved walls or complex geometries, LVL formwork adapts to the design requirements, providing the flexibility needed in modern construction projects.
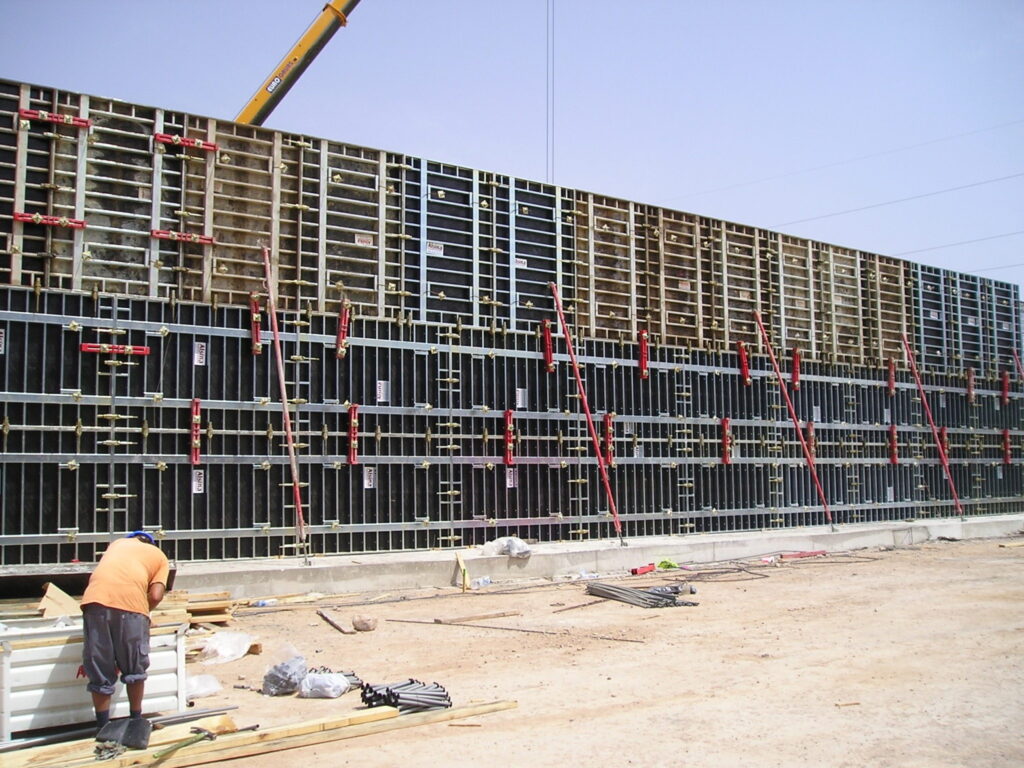
Key Components of LVL Formwork
To fully grasp the advantages of LVL formwork, it is essential to understand its key components. The primary components include the LVL panels, studs, wales, braces, and connectors.
The LVL panels serve as the main platform for the formwork, providing the necessary support and surface for the concrete. The studs act as vertical supports, ensuring the stability and integrity of the formwork system. The wales, on the other hand, are horizontal beams that connect the studs, distributing the load evenly across the structure.
Braces play a crucial role in maintaining the formwork’s stability during the concrete pouring process. They are strategically placed to resist lateral forces and prevent any deformation or collapse. Lastly, connectors are used to join the various components and ensure a secure and tight fit, minimizing the risk of leakage or misalignment. Read more about leakage at https://cedik.ca.uky.edu/industry-leakage-analysis
When all these components work together seamlessly, LVL formwork provides a reliable and efficient solution for concrete construction. Its versatility, durability, and ease of use make it a popular choice among builders and contractors worldwide.
The Advantages of LVL Formwork in Modern Construction
LVL formwork offers a wide range of advantages over traditional construction methods. These advantages contribute to increased efficiency, cost-effectiveness, and sustainability in modern construction projects.
Durability and Strength of LVL Formwork
One of the key advantages of LVL formwork is its exceptional durability and strength. The laminated veneer lumber panels are manufactured using high-quality timber, resulting in a material that offers excellent resilience and resistance to wear and tear. This durability allows for multiple reuses, reducing the overall material consumption and waste generated during construction.
The strength of LVL formwork is another significant advantage. The panels can support heavy loads and withstand the pressure exerted by the fresh concrete, ensuring the stability and integrity of the structure. This strength minimizes the risk of formwork failure, improving safety on construction sites.
Imagine a bustling construction site, where workers are diligently assembling LVL formwork panels. These panels, with their sturdy construction, provide a sense of security and confidence. The construction team can focus on their tasks, knowing that the formwork will support them every step of the way. The durability of LVL formwork not only saves time and money but also instills a sense of reliability in the construction process.
Efficiency and Speed in Construction
Time is of the essence in construction projects, and LVL formwork delivers in terms of efficiency and speed. The lightweight nature of the LVL panels makes them easy to handle and install, reducing the labor requirements and improving productivity. The formwork can be quickly assembled, allowing for faster construction cycles and shorter project durations.
Picture a construction site where the LVL formwork is swiftly put into place. The ease of handling and installation allows the workers to move with agility, ensuring that the project progresses smoothly. The efficiency of LVL formwork not only saves time but also enhances the overall construction experience, creating a seamless workflow that keeps the project on track.
Additionally, LVL formwork facilitates the use of pre-fabricated elements, further speeding up the construction process. The precision and accuracy of the formwork enable seamless integration with precast components, reducing on-site adjustments and ensuring a higher level of quality control. To learn more about reducing click here.
Environmental Impact of LVL Formwork
Sustainability is a growing concern in the construction industry, and LVL formwork addresses this challenge effectively. The use of timber, a renewable resource, as the primary material for LVL formwork significantly reduces the environmental impact compared to traditional formwork solutions.
Furthermore, the lightweight design of LVL formwork reduces the carbon footprint associated with transportation and installation. The formwork’s reusability further minimizes waste disposal and the need for continuous material production, contributing to a more sustainable construction industry.
As we strive for a greener future, LVL formwork stands as a testament to sustainable construction practices. By utilizing timber, a natural and renewable material, we can reduce our reliance on non-renewable resources and make a positive impact on the environment. The environmental benefits of LVL formwork go hand in hand with its practical advantages, creating a win-win situation for both construction professionals and the planet.
Comparing LVL Formwork with Traditional Methods
Now that we have explored the advantages of LVL formwork, let’s compare it with traditional formwork methods commonly used in construction projects.
Traditional formwork methods often involve using timber or steel, which can be costly and time-consuming. However, LVL formwork offers significant cost advantages that make it a preferred choice in many construction projects.
Cost Comparison
Cost considerations play a crucial role in construction projects, and LVL formwork offers significant cost advantages. While the upfront cost of LVL formwork may be slightly higher than traditional formwork materials, such as timber or steel, the long-term savings outweigh the initial investment.
LVL formwork’s durability and reusability result in reduced material costs over multiple projects. Additionally, the faster construction cycles and improved productivity associated with LVL formwork translate into cost savings in terms of labor and project duration.
Furthermore, LVL formwork is designed to withstand harsh weather conditions, reducing the need for frequent repairs or replacements. This durability factor contributes to long-term cost savings, making LVL formwork a cost-effective choice for construction projects.
Time and Labor Efficiency
Traditional formwork methods often require extensive manual labor and time-consuming processes. LVL formwork, on the other hand, streamlines the construction process, resulting in improved time and labor efficiency.
The ease of installation and adjustment in LVL formwork reduces the time spent on formwork assembly and modifications. This time-saving aspect translates into increased productivity, allowing construction teams to progress swiftly through different stages of the project.
Moreover, the lightweight nature of LVL formwork reduces the physical strain on workers, contributing to improved safety and well-being on construction sites. This not only enhances labor efficiency but also creates a more conducive working environment.
Quality and Safety Considerations
Construction quality and safety are paramount in modern projects, and LVL formwork excels in both aspects. The precision and accuracy achievable with LVL formwork result in consistent and high-quality concrete finishes.
Moreover, the stability and load-bearing capacity of LVL formwork ensure a robust structure, reducing the risk of accidents or structural failures. The inherent strength of LVL panels provides a level of confidence and safety assurance for construction professionals and stakeholders.
Additionally, LVL formwork is resistant to warping, twisting, and splitting, ensuring that the formwork remains intact throughout the construction process. This reliability factor enhances the overall quality and safety of the project, giving construction teams peace of mind.
In conclusion, LVL formwork offers significant advantages over traditional formwork methods in terms of cost, time and labor efficiency, as well as quality and safety considerations. Its durability, reusability, and ease of use make it a preferred choice for construction projects of all sizes. By opting for LVL formwork, construction professionals can achieve cost savings, improve productivity, and ensure the highest standards of construction quality and safety.
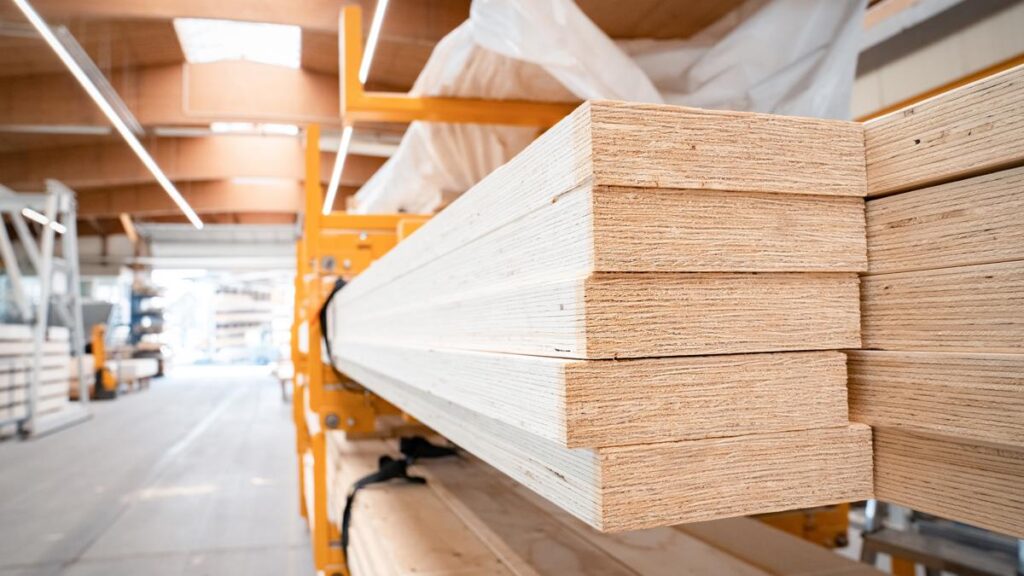
The Future of Construction: LVL Formwork
The future of construction is evolving rapidly, and LVL formwork is at the forefront of this transformation. Technological advancements and increasing environmental concerns present numerous opportunities for the adoption of LVL formwork in sustainable construction practices worldwide.
Technological Advancements in LVL Formwork
LVL formwork continues to benefit from technological innovations. The integration of digital tools and software solutions enables enhanced planning and optimization of formwork systems. Advanced modeling and simulation techniques allow architects and engineers to visualize the formwork design and make adjustments efficiently.
Additionally, the use of robotic systems for formwork assembly and concrete pouring streamlines the construction process and improves accuracy. These advancements in technology offer greater precision, efficiency, and safety, further cementing LVL formwork’s position as the preferred choice for modern construction.
LVL Formwork in Sustainable Construction
Sustainability has become a key driver in the construction industry, and LVL formwork aligns perfectly with this emerging trend. The use of timber as the primary material for LVL panels contributes to carbon sequestration, reducing greenhouse gas emissions.
Furthermore, the durability and reusability of LVL formwork minimize waste generation and promote circular economy principles. By incorporating LVL formwork into sustainable construction practices, the industry can reduce its environmental footprint and contribute to a greener built environment.
The Global Adoption of LVL Formwork
As the advantages of LVL formwork become more apparent, there is a growing global adoption of this construction technique. From residential buildings to large-scale infrastructure projects, LVL formwork offers a versatile and efficient solution for construction professionals around the world.
Learn more about formply on: The Best Formply Options Available in Australia for Your Construction Projects